Now known as the cheapest energy source in history, solar power has a lot of people wondering how a bit of silicon, metal and glass can be so energy efficient, cost effective and ‘green’ all at the same time.
So how is it done? The answer lays within the manufacturing process.
But before we can think about how solar panels are made let’s break it down and look at the separate materials it takes to make a solar PV.
Solar Panel Parts | What Are Solar Panels Made Of?
The most important part of the solar panel are the silicon cells. Silicon is a non-metal with conductive properties which is what gives it the ability to convert sunlight into electricity.
When sunlight hits a silicon cell it causes electrons to fire which creates a flow of electricity. This process is known as the ‘photovoltaic effect.’
There are three different types of solar PV cells used in solar panels. Once a silicon cell type is selected for the solar panel other elements are added for its construction. Check out what they are below:
Other base material used
- Metal Frame
- Glass sheet for casing
- Standard 12V wire
- Bus wire
- Plexiglass
Solar Panel Manufacturing Process | So How Are Solar Panels Made?
Monocrystalline and Polycrystalline solar panels have a similar manufacturing process. Below are the steps that are taken to transform these panels from a simple raw material such as sand to the solar panels we see on our rooftops.
1. Turning Sand into Silicon
The main material needed to produce a solar panel is silicon. Luckily for us, silicon can be found in natural beach sand which is an abundantly available resource on our planet.
Converting sand into high-grade silicon can be a tricky process however and requires costly, energy-intensive processes such as firing it through arc furnaces.
2. Developing Solar Ingots
Once the silicon has been created it is collected in its solid rock form.
Hundreds of these rocks are then melted together at very high temperatures to form cylinder-shaped ingots. To achieve the perfect cylinder shape the atoms are monitored to ensure they are perfectly aligned in structure and orientation.
Boron is then added to give the silicon a positive electrical charge.
*Point: Monocrystalline panels are manufactured from a single crystal of silicon, making it a higher efficiency rating. This is why the price of Monocrystalline panels is generally higher than other panel types.
**Point: Polycrystalline panels are made by melting a few silicon crystals together. This creates a shattered glass look on the finished product.
3. Slicing Solar Ingots Into Wafers
The next step in the solar panel manufacturing process is the cutting of the silicon ingot into ‘wafer’ thin disks.
Silicon is highly reflective, so it is also at this stage where an anti-reflective coating is added to the silicon wafer.
4. Developing Solar Panel Cells
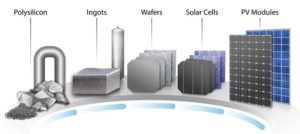
Now that the silicon wafers are ready, an electrical charge can be added to the system.
To do this, metal conductors are added to the surface of each silicon ingot wafer. These conductors are used to transform the wafers into a grid-like matrix to ensure maximum energy efficiency.
Finally, in a large oven, phosphorus is diffused over the wafers to help charge them with negative electrical orientation. The reaction between the boron (positive energy) and phosphorus (negative energy) gives the cell the power to function properly.
5. Final Solar Panel Construction
Now that the main component is ready, the solar cell can be put together and transformed into a tool that can convert solar power into electricity.
A solar panel is created by soldering multiple silicon cells together with metal. So how many cells are to a panel?
48 cells | Small residential panel size |
60 cells | Standard panel size |
72 cells | Large-scale panel size |
After the cells are put together, thin glass is added on the front side of the panel, the back sheet is made of durable polymer-based material and a junction box is added to enable the connection.
A solar PV is complete once the metal frame has been added.
6. Final Solar Panel Quality Test
All solar panels are tested under a 1000M/m2 irradiance light at 25 degrees Celsius to ensure it’s working correctly.
*Tip: Outcomes of this test can be found on the technical specification sheet of every panel.
The Best Method For Getting Solar Panels
The best way to get the solar panels that suit you is to compare quotes from multiple, experienced CEC accredited installers in your area.
Solar Market partners with top solar installers across Australia and will match you up with 3 local solar installers so you can start saving sooner.
If you need more help, take our 2 min quiz to find out what kW solar panel system you need and the costs involved.